Patent technology transforms lignin – a plant structural material – in aromatic hydrocarbons that could help jump on the synthetic aviation fuel “mixture wall”
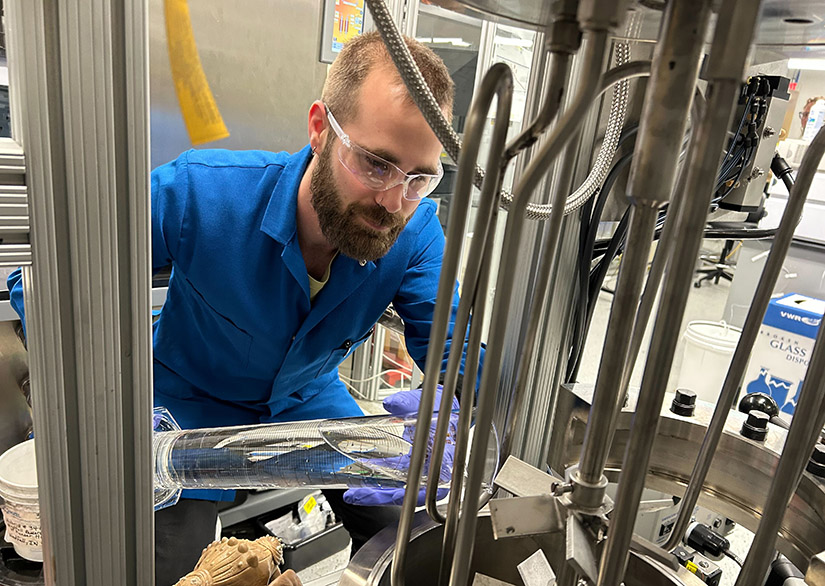
The research technician Nrel Spencer Lask is preparing raw materials for hydrodesoxygenation using a prize pressure reactor, going to the Nrel to operate in parallel with the part partner’s partner fuel. Photo by Mickey Stone, Nrel
It is an ideal complement to the own Comstock Fuelle technologies: an additional refining stage to improve the lignin of biomass in aromatic hydrocarbons, which are molecules necessary to produce “Drop-in” synthetic aviation fuel (SAF).
SAF can be made with biomass and abundant waste resources of American farms, forests and facilities. However, most SAF today must be combined with petroleum jet fuel (Jet A) to meet strict performance requirements for aviation. Indeed, jet engines need fuel which contains a mixture of hydrocarbons for safe operation – alcanes (including n -alcanes, isoalcans and cycloalcanes) and aromatics. To date, most SAF production processes have given fuels rich in N-Alcales and Isoalcanes, but the production routes of aromatics and cycloalcanes are rare.
But SAF technology being developed by the Massachusetts Institute of Technology (MIT) and the National Renewable Energy Laboratory (NREL) is different. It gives a SAF rich in aromatic by deconstructing lignin in plants and hydrodexygenation of molecules resulting from jet storage mixtures.
Understanding that SAF must include around 20% of aromatics, the president of Comstock feeds David Winsness jumped on the opportunity to extend the technology. In September 2024, Comstock Fuels signed a cooperative research and development agreement with MIT and NREL.
If the Mit-Nrel technology is successfully extended and integrated into existing Comstock processes, the combination of technologies could help approach the so-called SAF “mixture”-the supply of a path to SAF which is functionally identical to Jet A.
A fortuitous meeting of research sparks
Winsness discovered Lignine Mit-Nrel’s conversion technology in the process of patent at an exploratory meeting in Golden, Colorado, at the Nrel campus, where he discussed the scale of Bioleum SAF technology in Comstock. During this meeting, the main scientist of the Nrel, Robert Baldwin, presented Winsness and his colleagues to the new Chemin de Lignine and recommended an introduction to the main research NREL Gregg Beckham and chemical engineer Nrel and group director David BrandnerWho directs Nrel’s component together with a team of researchers.
Veteran of the biofuels industry, Winsness had itself developed and marketed a patented process which recovers the corn corn oil from corn ethanol installations for use in the production of additional fuels, the increase in yields and income. Over 95% of the American corn ethanol industry uses technology today. Winsness and his team then turned to lignin as their next innovation on the conviction that it could support oil, pulp and paper, forestry and other relevant industries.
After more than 10 years, they have developed a patented and patent process which extracts and converts the lignin into intermediary called Bioleum. In a press release of August 2024, the company reported yields of cellulosic ethanol and combustibles derived from bioleum exceeding 125 gallons per metric ton of biomass (on an equivalent basis for petrol-gallon), depending on the raw material, the linen content, site conditions and other process parameters.
After the initial introduction of Baldwin to Beckham and a series of follow-up communications, it has become clear that SAF technology based on Mit-Nrel lignine could complement the comstock processes by further refining the Bioleum to produce both Alcane and Aromatic SAF. The parties recently made an exclusive license agreement, in addition to the research agreement, only six months after their first meeting.
In its pilot installation in Wisconsin, Comstock Fuelle is currently on the scale and demonstrates its Bioleum technology to convert Woody biomass into SAF. A stage of the chemical processes of Comstock isolates lignin by separating it from the other main plant polymers – cellulose polysaccharides and hemicellulose – which continue throughout the conversion process in Alcane SAF.
“The type of digestion we are already doing is ideal for MIT and Nrel technology,” said Winsness.
He was there – where Comstock produced a flow of lignin – that Baldwin and Winsness have seen an exciting interdependence and liaison point.
“MIT technology and Nrel manufactures a very aromatic mixture, but it’s great because most other SAF technologies are today made with mixtures that do not contain aromatics,” said Baldwin. “To get 100% SAF, you must have a source of aromatics, and a way of obtaining them is Lignine.”
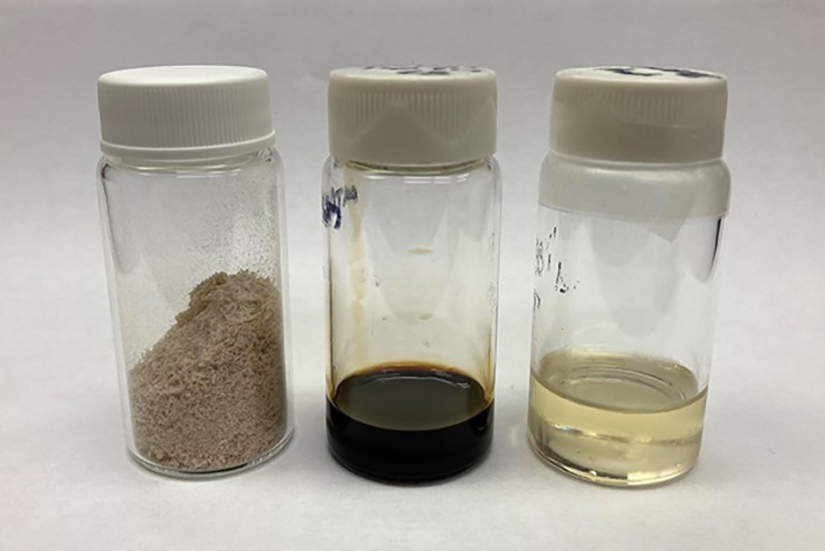
From lignin to highly aromatic SAF
Lignine – which represents around 30% of biomass – is a complex polymer that supports plants and helps them withdraw disintegration. On the basis of projections of the future supply of raw materials, which are described in the 2023 billion tonnes of the US Energy MinistryLignine could generate up to 63 billion gallons of SAF each year by 2040, three times more fuel than American airlines consumed in 2019.

However, for years, the industry does not have the key to unlocking this potential. Researchers continue to seek economic methods to transform lignin into useful products, including aromatic hydrocarbons necessary for SAF. In the pulp and paper industry today, lignin is burned for heat, although Nrel and other researchers are also developing
Technologies to transform the lignine of waste into precious bioprodits.
However, based on the advances in catalysis, a team of multi-institution researchers, including Mickey Stone of MIT, Matt Webber and Yuriy Román-leshkov, unveiled a study with the potential to overthrow this dynamic. With the support of the bioenergy technology office of the American energy department, they have demonstrated a method to eliminate oxygen from lignin and a catalyst to refer the resulting molecules in a SAF mixture rich in aromatic – an additive to mix with Alcane SAF.
Described for the first time in a 2022 Joule articleTechnology combines alcohol extraction of biomass lignin with a hydrodeoxygenic catalyst in terms of land to stabilize the extracted lignine and produce oil enriched with aromatics. Above all, this catalyst resists the deactivation or poisoning of impurities often present in biomass.
After successfully demonstrated technology in the laboratory, MIT and Nrel have made a patent application for technology. Now, to show its value outside the laboratory for the biofuels industry, it is time to make it evolve.
The three -year plan: failure
Over the next three years, Comstock will create a pilot version on a pilot scale of Lignine Mit – Nrel, a task which consists in connecting the different stages to an uninterrupted process that can be carried out continuously. They will also incorporate larger reactors and equipment, going from the production of Milliliters of the Aromatic Blendstock SAF to a few gallons.
This process will provide precious data and engineering conceptions to Comstock to Comstock as it works to integrate it into its own Bioleum technology. Winsness said that the Mit-Nrel process can be added with some minor modifications to accept the existing lignine flow.
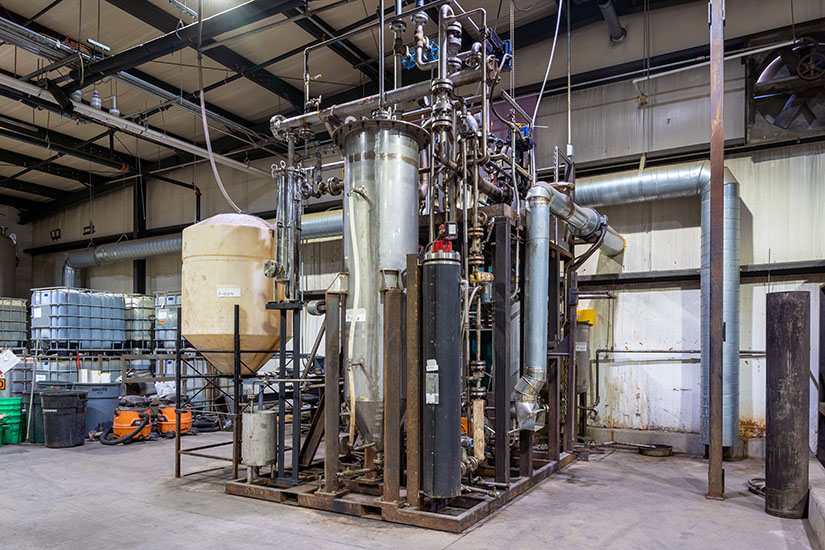
“We already have more than 2,000 points on our pilot reactor and a huge amount of data,” said Winsness. “We think we can take the Mit-Nrel process from a level of technology preparation (TRL) from 4 to 6 very quickly if everything is going well.”
Of course, it would not be the end of the systematic process to demonstrate and market technology. After having managed to manage the Mit-Nrel process at TRL 6 and 7, Comstock should then integrate the process into even larger facilities in the coming years, raising the Comstock and Mit-Nrel processes at TRL 8 and 9. Comstock Fuil Pland Installation-pave the way for marketing.
Success could put millions of SAF gallons on the market, according to Eric Payne, director of senior licenses in Nrel.
“It is not every day that the laboratory obtains a partner like Comstock which is ready to jump and finance the scale of technology, which is so critical for marketing,” he said. “They have the potential to have an impact on billions of gallons of SAF, and it’s really exciting. It’s a huge market. ”
Learn more about Research on biofuels and organic chemicalsas well as the widest in the laboratory Advanced aviation search.