At Amazon, our delivery stations can be the smallest buildings in our operations network, but they play a crucial role to guarantee that our customers receive their orders on time and in good condition. Every day, these installations run around 40 operational processes to prepare thousands of packages for delivery to customers of neighboring communities. Employees receive the packages, sort them on the final delivery route, pack them in bags and prepare these bags to recover by our delivery service partners. To make these jobs safer and easier, we expect to have invested more than 700 million euros in technological innovations in our European delivery station of 2021 at the end of 2025.
Why now?
While we look to the future, we want to make sure that we create more skilled work that is ergonomically healthy for young and aging populations. Technology helps us achieve this vision.
In recent years, we automatize physical and repetitive tasks in our realization centers, building the largest world fleet of 750,000 industrial robots that collaborate with our employees. Our growing scale and our expansion of use cases have contributed to reducing technological costs, allowing us to implement robotics and automation in other parts of our operations, such as our package delivery network.
Transforming delivery stations with technology
When we started delivering packages to customers in Europe in 2012, most of the operational processes in our delivery stations were manual, with limited technological support. Since then, we have developed, test and implement innovations that create better and safer work environments while allowing faster delivery.
We have opened the Last Mile Innovation Center in Dortmund, Germany, which serves as a single world test establishment where we develop technologies that will shape the next decade of our delivery company. Here, we have successfully tested the concept of the “delivery station of the future” and we expect the first fully operational delivery station in accordance with this concept of launching in 2026 in Europe.
Here are some of the innovative technologies that will support employees and manage the most repetitive physical tasks:
Lord
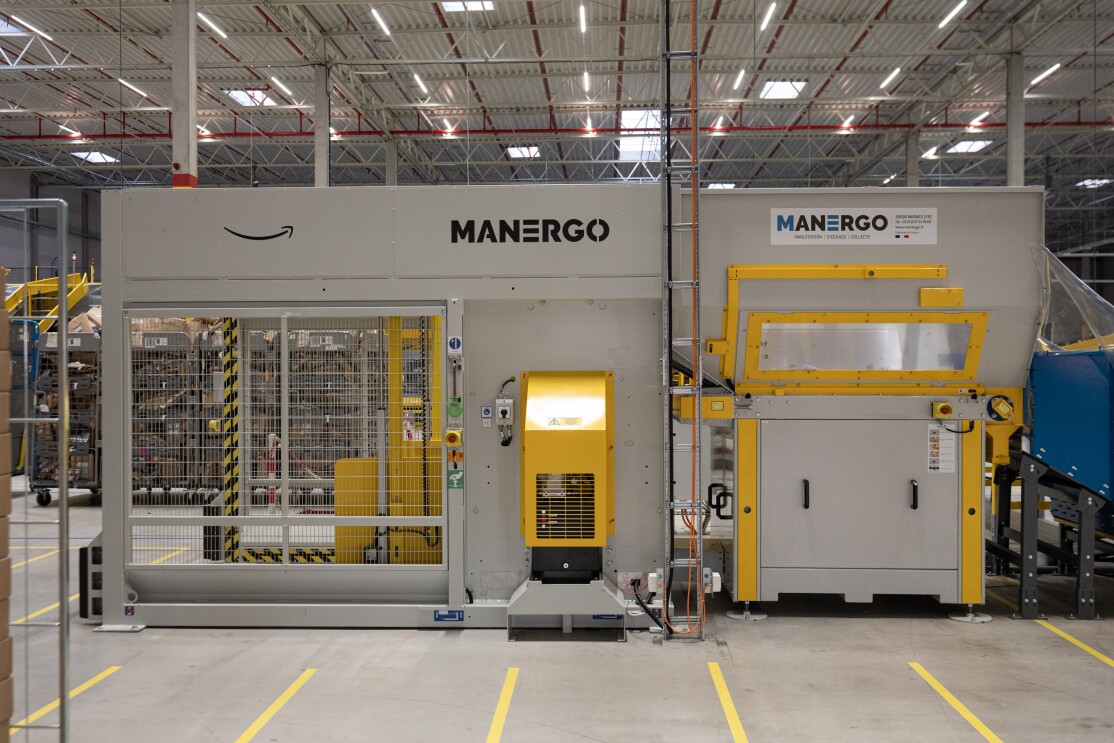
An automated solution that eliminates the need for manual unloading of the package. Instead of physically removing the parcels from the carts, the employees simply bring carts to this innovative system, which automatically transfers packages on the treadmill. This technology considerably reduces physical constraint while maintaining an effective package flow.
Echelon and scanner with six sides
These two complementary technologies work in perfect harmony. The level system manages the package flow on conveyor belts, while the six -side scanner automatically captures information from the package from all angles. Together, these innovations eliminate the need for manual digitization and handling, creating a more rationalized process.
Agility and matrix
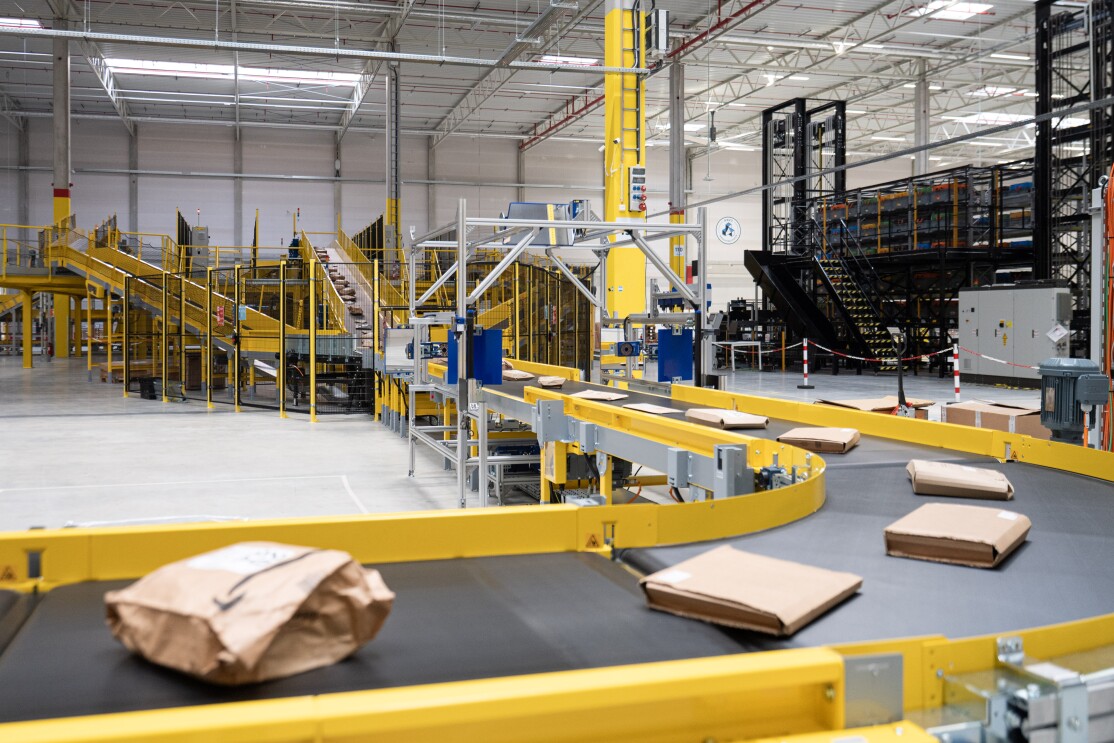
These sophisticated technologies determine optimal paths for sorting packages. They minimize the need for employees to push, reach or manually manage packages, creating a more efficient and ergonomic working environment.
Zancasort
A transformative technology that brings packages and their bags directly designated to employees at an ergonomic height. With this technology in place, employees no longer need to browse many alleys or reach to stack plots. They simply place packages in their designated bags, which makes the process more efficient and much more comfortable.
Sorting station assisted by Vision (Vass)
This innovation uses computer vision and projection technology to help employees sort the packages more effectively. It visually puts the packages and their correct sorting locations, which a lot facilitates employees to quickly match thousands of packages with good delivery route bags.
Create new opportunities
These innovations do not mean that we have slowed down the hiring. Since the introduction of robots in Amazon operations, we have hired hundreds of thousands of employees to work in our facilities. And we continue to invest in skills training programs, because instead of making manual task sorting packages, this person can be trained to use the technology that provides support.
In 2024 only, more than 20,000 employees in our European delivery station network acquired new skills related to operational automation technology and innovations fueled by AI. In addition to this, our employees can choose to develop certain skills. Our pre-paid career choice skills training program Funding for national-recognized courses to meet current and future employment needs for thousands of employees. Our data show that almost 30% of participants active in career choice in Europe are registered in technological implementation courses and it is the most popular path among our employees.
The deployment of technology also means that we need people to design it, create its software, control and maintain it. Over the past two years, we have increased the number of employees of the delivery station in reliability, maintenance and engineering roles in Europe by more than 50%.
I am incredibly proud of the progress made by our teams since the launch of our last mile network in Europe in 2012. We remain determined to invest in technology that creates better and safer jobs and accelerates customer deliveries.