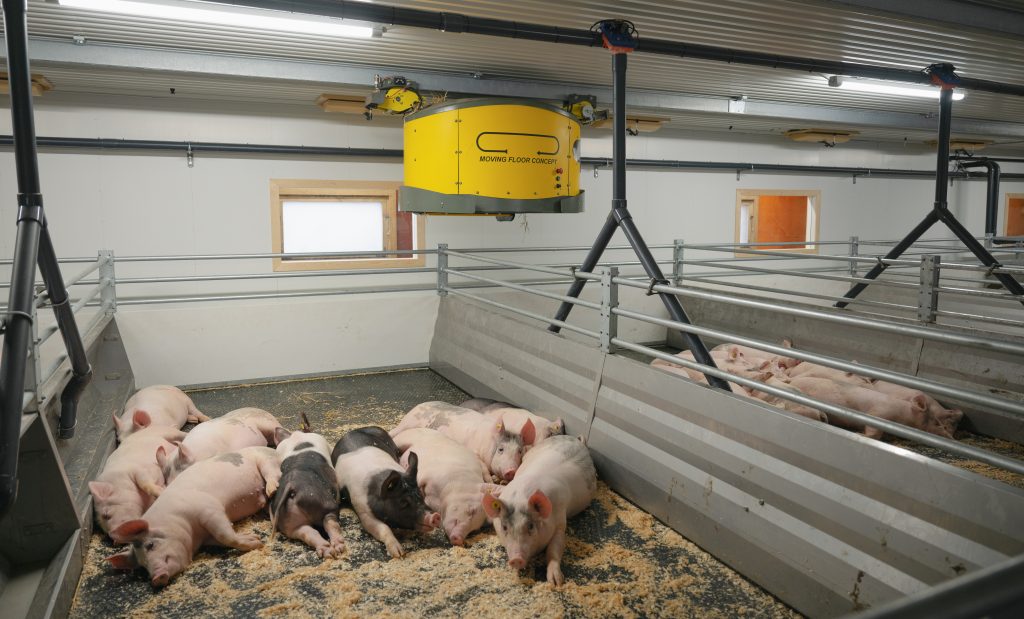
Emissions3-RFP-051925
With around 1 billion pigs worldwide, the pork sector produces large quantities of emissions per year which are now excessive from the government with reduction objectives.
Due to the intensity of their production system, pigs emit significant levels of ammonia and greenhouse gas in their excrement and urine, which accumulates in the barns.
Pork being the most consumed meat in the world, representing more than 36% of the total meat consumed, more pork housing is erected to meet demand, but this also means an increase in emissions as collateral damage.
However, a company in Sweden examined this trend and designed the ultimate technology to help reduce emissions in the form of housing modules with rotary floors.
Much named, in motion, the company was founded and belongs to two sisters, namely Peg Soderberg and Katja Lindvall, with Soderberg as CEO.
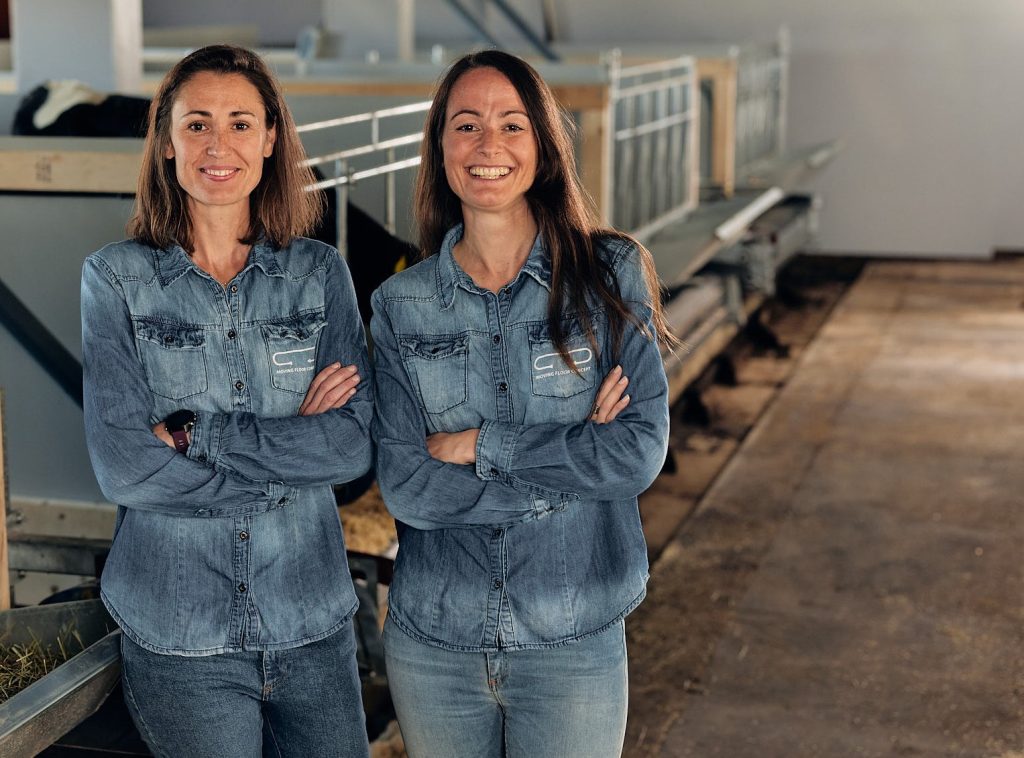
The company is based on the Swedish island of Gotland and has developed housing modules, initially for calves and pigs, with continuous moving soil that is effectively cleaner by scraping manure and urine.
The conveyor belt floor is powered by an air compression requiring eight bars to operate at previously fixed time intervals.
The company claims that this system can reduce ammonia emissions in the pork barn up to 85%, compared to the normal pork housing.
The module weighs 1,200 kilograms, measures 5.4 m per 2.4 m, covering an area of 11.6 square meters and is 1.6 m high. It is a wooden structure covered with stainless steel with average energy consumption of less than 100 kWh / pork / year.
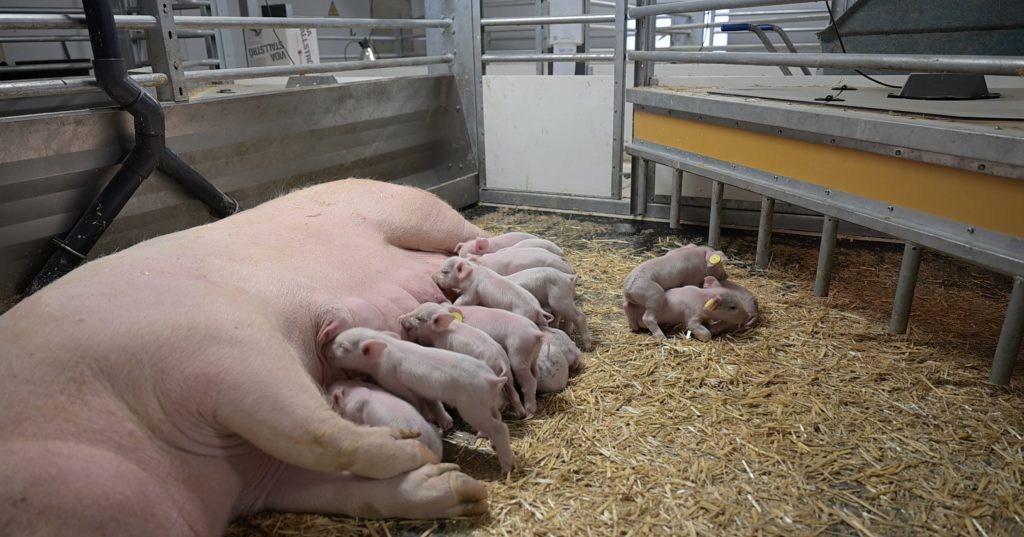
Demonstration barn
As part of a project funded by the EU, Moving Floor welcomes demonstration barns with its technology integrated into a farm outside of Vastras belonging to Tobias Pettersson producing 8,000 fattening pigs per year.
Soderberg said: “The moving floor has renovated parts of the farm and operates our technology in four barns there; A keel unit holding 12 sows, a nursery unit and two finishing units.
“In these barns, we execute the soils cleaned automatically as well as our automatic bedding machines, and we digitly measure ammonia emissions every 15 minutes.”
The turning floor, pork excrement is removed within two hours of defecation of a pork. With the excrement withdrawn, the aerial litter robot can offer straw or sawdust, as programmed to do so.
The deployment of the floor uses a number of different tests in the barns to see how effective technology is.
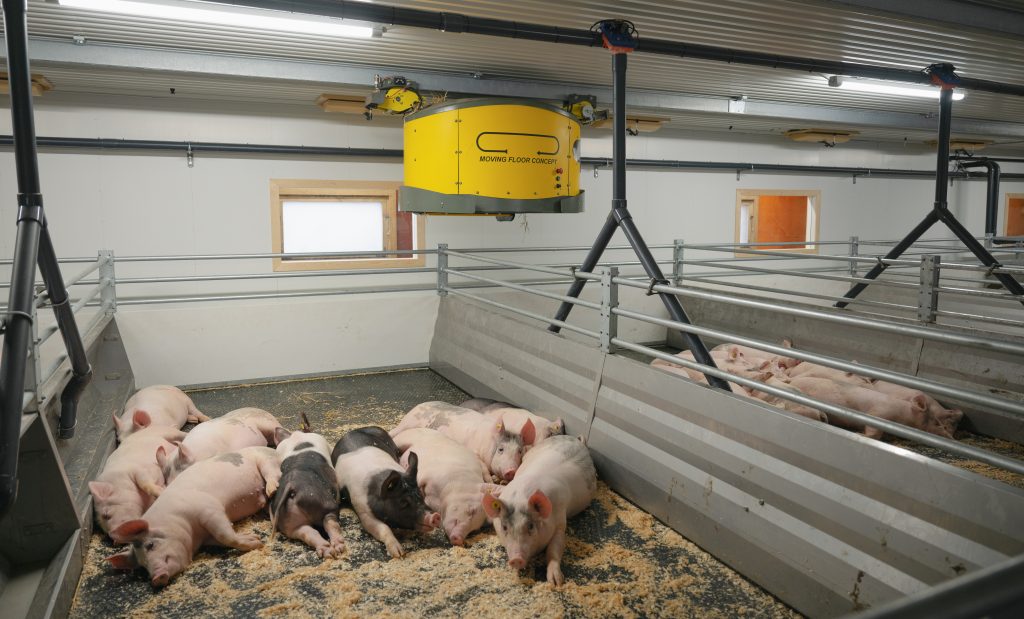
Soderberg said: “We take measures according to the Vera protocol which means ammonia, dust and smell. In addition, we pilot a composting drum for manipulation of manure with the idea of closing the nitrogen loop as much as possible.
“Since we have a rapid elimination of the barn excrement, we can minimize ammonia emissions in the barn, preserve nutrients in manure and strive an energy -efficient process of manure in a chemically stable organic fertilizer which can be distributed in the fields.
“We have marked and took more than 17,000 photos of the pigs, following them from birth to slaughter. The photos are annotated by Professor Mate Zoric in SVA, a veterinary institute of the State, and marked according to the conditions of hooves, knees and belly.
“SVA also participates in the analysis of the disease and the consumption of antibiotics. An analysis of the climate impact will be carried out by the IVL, the Swedish Institute of the Environment.
“We are already seeing indications for dropping ammonia emissions, pointing to reach the lens of only 1.1 kg per placeur per year. The concentration of ammonia in the barns extends from 2 to 5 ppm in general, which is a good perspective of animal welfare,” she said.
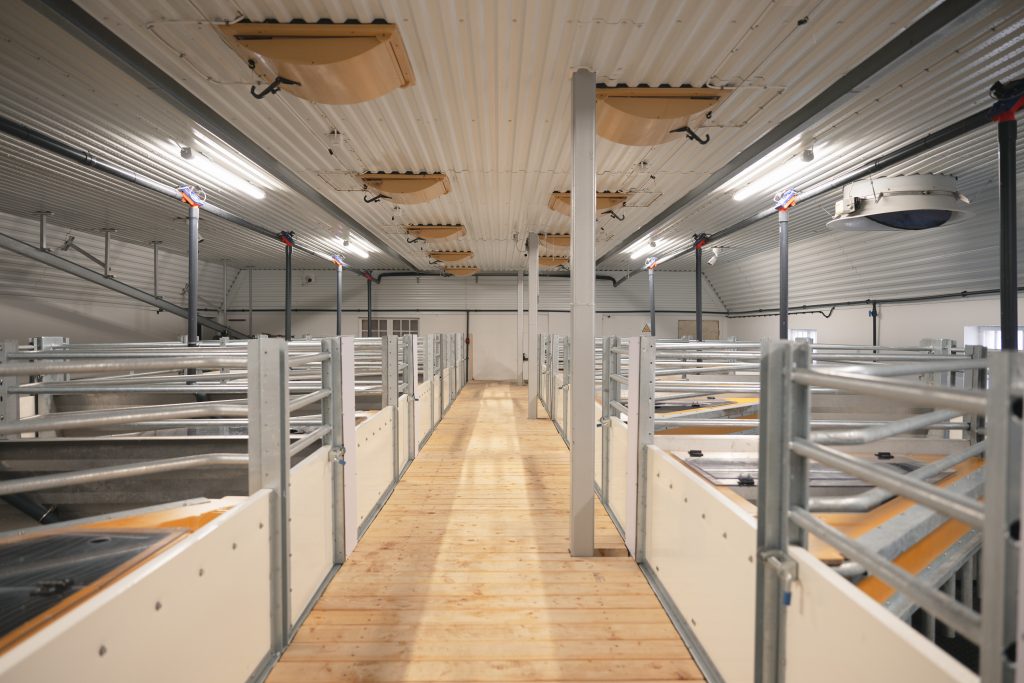
Improvement of animal welfare
The moving floor modules can improve animal welfare in terms of supply of solid floors which can support the use of litter and enrichment materials. In addition, the storage density can be varied, without affecting the cleanliness of the soils.
The company says that all of this can play a major role in stopping the tail mooring and providing a system more in line with consumer demands and expectations.
The moving floor system can be installed either in new barns or in older established units. Animals kept under clean and hygienic conditions have better chances of performance in terms of daily food conversion and growth rates.
Compared to the concrete floors of scratch manually, the backup of work with the rotary floor modules is significant, and also for the distribution of bedding.
The move says that its objective is to provide automatic cleaning for barns and to make it become a new standard of industry.
Soderberg added: “We hope that the moving floor can play a role in a rapid transition from European farms to more sustainable and oriented towards animal welfare.
“For the future, we are working on an intelligent system to execute the floors according to ammonia emissions. Basically, we define the authorized level of ammonia emissions on the specific farm and allow the system to operate and optimize automatically depending on the algorithms.
“This will also allow farms to generate reports that can be sent to control organizations, to comply with ammonia regulations.”
The moving floor indicates that the average reimbursement of its system is three years. The company has already installed units in Europe and China and speaks to potential customers in other regions.
